Turning theory into reality
In the R&D stage of this project, each panel was created by hand in our lab using dedicated machinery and specialized measurement instruments.
Making VIPs with polyurethane cores
With this process, the cores are preformed, but must be cut to the correct size. It is then placed into an oven to remove any excess moisture. As an additional preventive measure, a chemical moisture absorber is inserted into one corner before applying the vacuum which uses heated blades to seal the core within the multilaminate film.
Benefits
- Higher insulating capacity (2x-5x) with respect to traditional PU foam
- Excellent lambda value (6-7 mW/m/K)
- Possibility to create 3D shapes
- 4x lighter than commercial VIPs
Making VIPs with recycled polyurethane
The recycled polyurethane is obtained by grinding rigid foam, in this case taken from end-of-life refrigerators, and reusing the resulting powder to create a new panel. This powder is blended with an additive and placed into a heated mold to form a core. Once molded, the core follows the same process as the standard panels above.
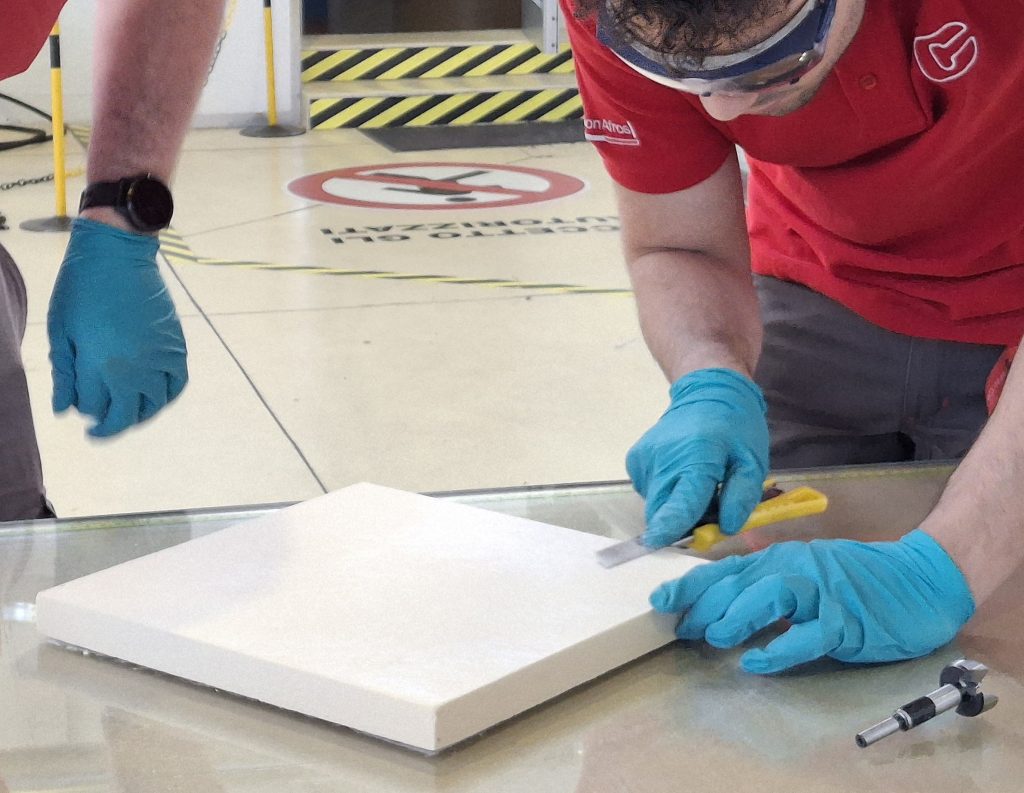
Final steps
The last step for each panel, regardless of the production process, is to measure its lambda value. Both types of panels displayed excellent lambdas (6-7 mW/m/K), and a host of other benefits compared to traditional VIPs.
To get a complete look at each process, scan the QR code and watch the videos.
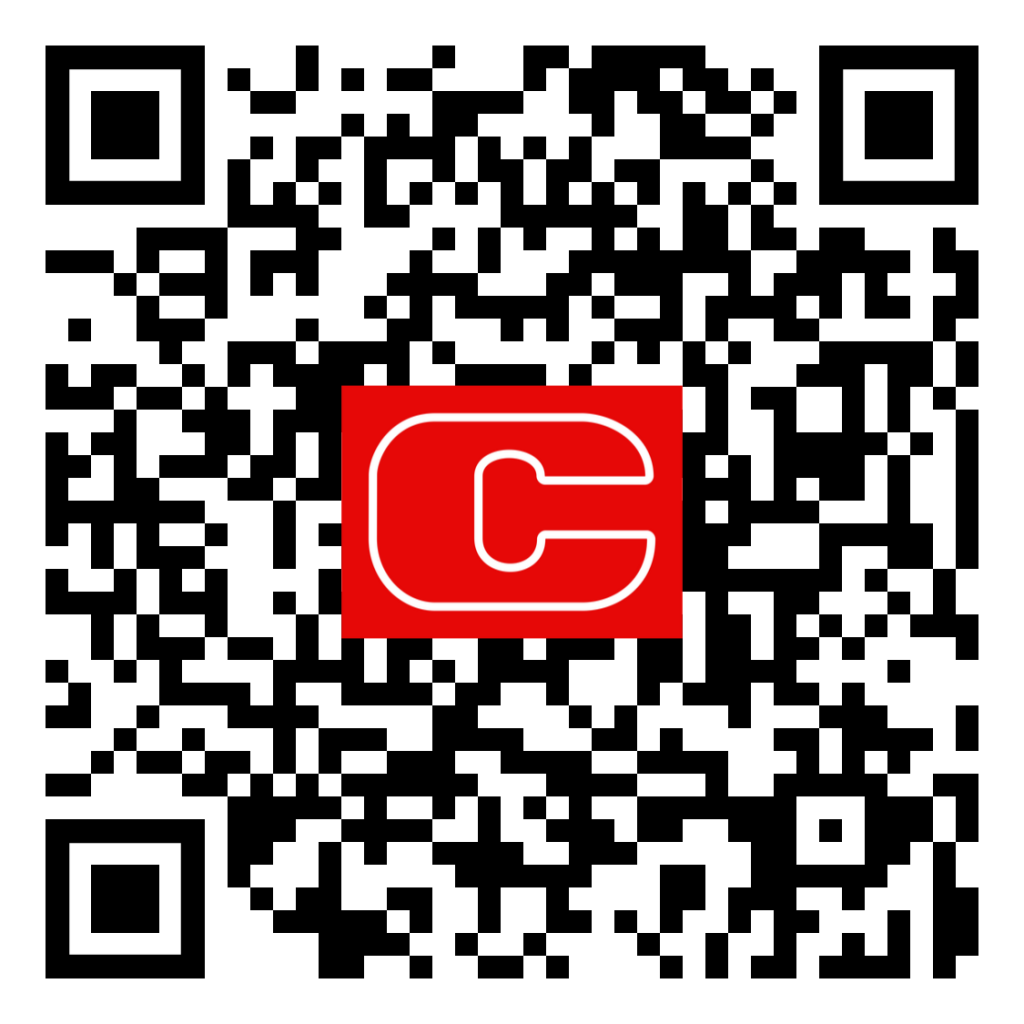